Vacuum Chucking –Essential for Modern Industry
- Sheldon Thompson
- Nov 11, 2019
- 4 min read
Updated: May 6, 2024
A discussion of the benefits of Vacuum Workholding in the manufacturing industry from the Magna-Lock USA archives
How do you hold nonmagnetic exotics, thin strips, and delicate workpieces? Atmospheric pressure can do it without deforming or marring surfaces. It’s just as dependable as gravity, and it’s powerful, too. There are 14.7 lbs. of air pressure for every square inch at sea level; and we can get sufficient vacuum in a chuck to generate about 13lbs./square inch holding power. That’s over 1,100 lbs. for a workpiece the size of a standard piece of paper. Here’s how to use this free force.
To meet challenges of holding exotic alloys, sophisticated products, and machining them to tolerances in ten thousandths of an inch, tool engineers are turning to vacuum chucks to supplement or replace mechanical and magnetic chucks. The vacuum chucks perform hold-down and positioning functions heretofore impossible. For example, dramatic results are being obtained in holding plate glass for polishing on a high production basis for the automotive industry. Elimination of hold-down clamps solves the breakage problem and leaves the entire surface unobstructed for polishing the edges.
Processing of ultra-thin foil, plastic, and shim materials as thing as 0.0005” is possible too, and it can be done with large-are sheets without wrinkling or patterning.
Similarly, the uniform distribution of vacuum pressure over the entire area of the workpiece makes it possible to produce highly polished surfaces with uniform thickness. The machine designer and tool engineer can have practically unlimited design freedom as far as size is concerned. Vacuum chucks are holding workpieces from 1 square inch to 20’ x 60’.
The instant hold and release of vacuum chucks adapts them well for high-speed automatic CNC machines. The use of instant-acting fail-safe switches protects machines, materials and operator. The vacuum chuck has wide versatility for all types of machines and operations including milling, drilling, profiling, broaching, grinding, sanding, and polishing.

Fixture Design
When irregular shares are involved, fixtures are readily designed and easily made to accommodate the workpiece. The vacuum fixture eliminates complicated mechanical clamps that would require costly forming and machining under toolroom conditions. The vacuum can perform the dual function of holding the work and anchoring the fixture to the machine bed.
The minimum thickness of the vacuum chuck, normally only 3⁄4” to 1 3⁄4”, permits maximum working clearance of the machine for large pieces or large-diameter arbor-mounted cutters. Chucks can be arranged with grooves, manifolds and seals to take workpieces of varying sizes and shapes.
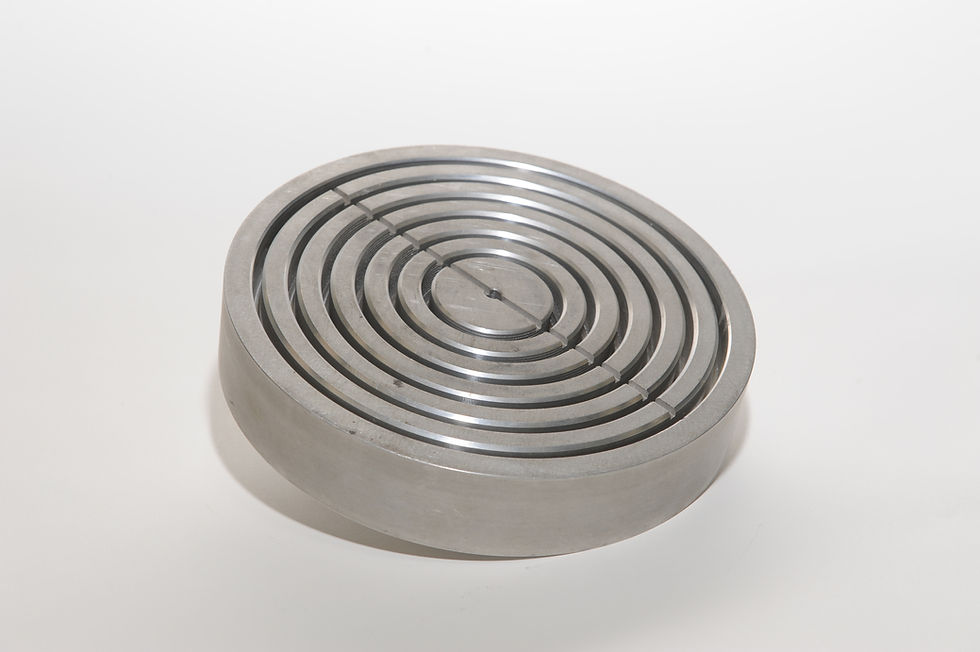
Holding Power
Calibrated orifices provide negative pressures up to 13 lbs. per square inch, supplying tons of hold-down force on large areas. A small 1” square has a 13 lb. force, but a square just 2” x 2” has 52 lbs. The area multiples fast! Various groove patterns are available to suit the type of work and seals are easily and quickly changes to fit the size or number of pieces to be held.

Variety of Applications
Vacuum chucks can be adapted easily to almost any standard machine for either permanent or temporary use. In the case of a bed with “T” slots, steps are machined in each end or side so the unit can be bolted down. For magnetic chucks, a steel plat e is bolted to the bottom of the vacuum chuck, making it possible for the magnetic chuck to hold it.
For the solid bed machine, an open-back vacuum chuck is used. It will hold itself down as well as hold the work when the vacuum is turned one, or it may be bolted in place permanently.
A vacuum chuck may hold any number of pieces at one time by merely having more vacuum ports. Of course, these extra ports must be covered or turned off when they are not in use. This can be done on a groove pattern by placing a small strip of gasket material over the vacuum ports in the bottom of the grooves. Also, when the chuck is designed, each individual set of ports can be manifolded to an outside valve and merely shut off.
Vacuum is supplied by a standard pump, sized to fit requirements. Controls can be automatic, and a fail-safe switch can shut down the machine automatically in event of the power failure or loss of vacuum.

Engineering services are available as an aid in solving problems ranging from simple to complex integrated vacuum systems.
Engineering Guide
It is best to design the chuck with characteristics that match the individual operation. Although a grooved pattern chuck is the ideal for versatility and holding power, it falls short when the stock to be machined is thinner than 0.0015”. In cases like this, a herringbone pattern may be used, or a small-hole pattern will serve. However, the hole pattern will not hold warped pieces, and it will not maintain as great a holding power. Thus, on production run material, it is often better to have a chuck designed for the specific job.
Engineering services are available as an aid in solving problems ranging from simple to complex integrated vacuum systems. Contact our sales team today to further discuss how vacuum workholding can work for you.
Versatility and economy are important advantages of vacuum chucks.

Obsidian Manufacturing Industries, Inc. is a Rockford, Ill. manufacturing company and is the OEM for Magna-Lock USA workholding, MagnaLift & Power-Grip lift magnets, and Arter Precision Grinding Machines as well providing surface grinding services. They are located at 5015 28th Ave. in Rockford, Ill. with a phone number of 815-962-8700. Check out more at obsidianmfg.com/brands.
Comments